Together with Wirthwein SE, KraussMaffei has won first place in this year's AVK (German Federation of Reinforced Plastics) Innovation Award for fiber-reinforced composites in the Processes & Methods category. The award was given to the newly developed CFP (Chopped Fiber Processing) technology. The new technology for direct compounding of chopped fiber in the injection molding machine yields significant material and energy savings compared to continuous-fiber-reinforced technologies.
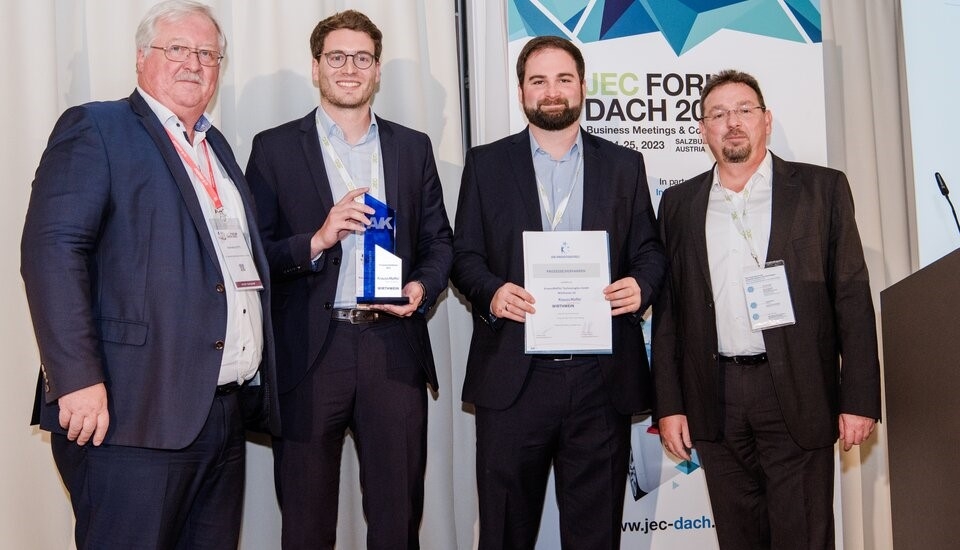
Depending on the component, up to 46 percent of material costs and approximately 0.8 kWh per kilogram of processed material can be saved. Transport and storage costs are also reduced. The investment costs for precompounding are unnecessary. In particular, the reduction in energy consumption during processing and the reduced transport routes lead to a significant reduction in the CO2 footprint.
For the greatest possible cost-saving effect, particularly large shot weights are preferred, i.e. large-volume PP-GF components. Conceivable applications are, for example, in the automotive industry in the interior and in the engine compartment, for example for door modules, front ends, dashboard panels, fan frames or engine covers, as well as in other industries such as technical parts as well as packaging and logistics. Another advantage of the new CFP technology is that recyclates can also be processed safely.
Patented screw for easy retrofitting
The heart of the new CFP technology is a screw specially developed and patented by KraussMaffei that ensures a high degree of blending of fibers and polymer matrix and prevents fiber clusters. The patented screw can be retrofitted without any problems. The fibers are metered directly into the plasticizing unit together with the polymer granulate and additives. Thus, precompounding is no longer necessary.
The new CFP technology now makes it possible to manufacture fiber-reinforced components from chopped fiber with the same component properties as those from continuous fiber processing methods. This is associated with a significant reduction in machine, material and energy costs.
Felix Weitmeier (Teamlead Process Engineering KraussMaffei)
“The new CFP-process has the potential to replace the use of more expensive processes for continuous fiber processing in many cases.”
The options to create its own recipes optimized for the respective application makes it possible for Wirthwein to produce customized products for its customers.
Jan Wiedemann (Head of Innovation and Materials Wirthwein)
“This minimizes overengineering of the materials and thus cuts costs and CO2 emissions, boosting competitiveness significantly.”
The renowned Innovation Award for fiber composite plastics of the AVK– Industrievereinigung Verstärkte Kunststoffe, a German plastics industry interest group, is given each year in three categories for outstanding composites innovations. An expert jury composed of engineers, scientists and industry journalists evaluates the submissions based on criteria such as level of innovation, degree of implementation and sustainability.