This year, Guilin Rubber Machinery has been active in responding to market changes and seeking for cooperation with prestigious companies in developed countries by taking opportunities presented by company restructuring, quickened the pace of meeting the requirements of the international market, and strived to improve its ability to expand development space and increase revenue. To improve the production and work environment, the company has not only improved the appearance of plants, workshops and offices, but also worked hard to better the qualities of employees, help them foster good habits, and boost their morale, laying a solid foundation for improving the quality of products.
In recent months, the company has stepped up to improve the production and work environment, including the interior walls and floor of each workshop. The 6S management has been dutifully applied at the production site to improve the corporate image and product quality. The environment improvement pilot project was launched at the export work section of the assembly workshop, producing remarkable improvement. The company has decided to launch the 6S evaluation and inspection campaign in the second half of this year, issued related administrative measures to advance the work, specified the rules on how to place all sorts of routine office hardware facilities inside the offices and sent the inspection group to make irregular checks per month. The above practices have become routine in the past months and helped foster good work habits among the staffs.
The company also advances the SHE management in a comprehensive and in-depth way to protect the safety and health of employees. Necessary improvement has been made to the work environment in three major workshops. Specifically, at the assembly workshop, the painting process is optimized at the assembly workshop, with paint spraying moved to the spray & baking booth to improve the paint spraying quality and the nearby work environment. The floor inside and outside the rivet weld workshop has been hardened to improve the work environment and reduce dusts. What’s more, a set of circulating water dust removal device has been added to the shot blasting machine in the shot blasting room to suppress the dust and protect the environment. At the end of last year, a flue pipe was extended to the metalworking workshop to improve the traditional cooling methods for cuttings, reduce the cost and enhance the efficiency and the work environment. The above eco-friendly measures have produced initial effects and are warmly welcomed by employees.
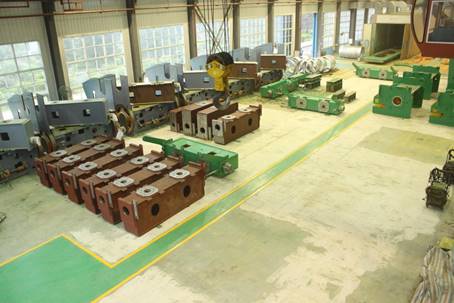
The improved accessories plant of the assembly workshop
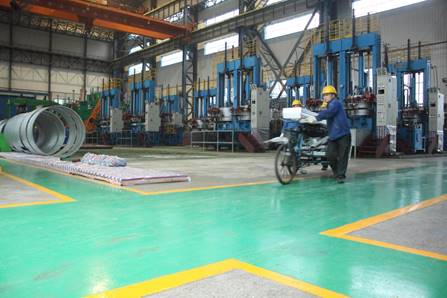
A corner of the improved heavy machinery workshop
(Written and photo by: Li Li)