(Hannover, February 21, 2022) When searching for the ideal production technology for the newly founded pipe manufacturer Encoma Ltd in Manitoba, Canada, plant manager Derek Hofer had clear goals in mind: no simple me-too products, but efficiently produced, high-quality HDPE pipes. With the first QuickSwitch line in North America delivered and commissioned by Hannover-based KraussMaffei Extrusion GmbH, the industry newcomer found the perfect solution to translate these goals into reality. Two additional production lines have already been ordered.
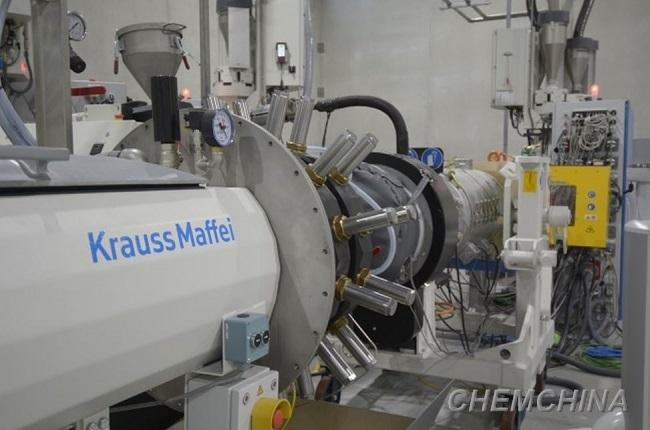
Encoma started manufacturing multilayer HDPE pipes for water supply, geothermal and cable protection applications as well as for underfloor heating in the fall of 2021 after building a new factory accommodating several extrusion lines in Manitoba. Within the frame of this project, KraussMaffei Extrusion installed a complete 3-layer QuickSwitch line covering the entire production process – from raw material to semi-finished product handling. “For us as a newcomer in this branch of industry, it was extremely important to have a competent partner at our side who would be able to set up a turnkey plant on our premises and also provide training and support,” says Derek Hofer, Plant Manager at Encoma. He adds that there is absolutely no reason to regret the purchase decision because KraussMaffei has fully met all expectations. What’s more, Encoma is so satisfied with the plant technology and machine supplier that the company ordered two new lines just three months after the start of production – a second QuickSwitch line and a 5-layer PE-RT line specifically designed for underfloor heating pipes. “Quality, reproducibility and production time achieved with the first QuickSwitch line for HDPE pipes were so convincing that we decided to go straight back to KraussMaffei as our machine supplier,” explains Derek Hofer.
Pipe dimensions adjusted at the touch of a button
QuickSwitch is the name of KraussMaffei Extrusion's unique package solution for the flexible production of pipes of widely differing dimensions on one line without requiring any retooling. The core component of each QuickSwitch line is the adjustable calibration basket, which is set to new pipe dimensions fully automatically and within a given time without having to stop the production line. The waste produced during the “quick switch” period is limited to a cone-shaped piece of material, which contributes not only to higher efficiency but also to enhanced sustainability in hose production. In addition to changing the pipe dimensions at the push of a button, QuickSwitch also ensures fine adjustment of pipe wall thickness and pipe centering. Both parameters are of fundamental importance for the production of high-quality pipes. Once saved, production data can be retrieved and adjusted at any time, which ensures exact reproducibility. The entire downstream equipment integrated into the control system is automatically adjusted as well, readjustment is therefore no longer necessary. Thanks to the intelligent control system, all production parameters can be monitored, documented and correlated with each other. The line thus manages itself and the personnel effort is minimal. All in all, QuickSwitch is the ideal solution for newcomers in the market like Encoma. With the line already installed at the Manitoba site, Encoma produces pipes with diameters ranging between 25 and 63 mm. The line now ordered will extend the dimensional range up to 6 inches (168/175 mm). „Thanks to the perfectly tailored machine solution, we are able to produce a wide range of different pipes for changing customer requirements even in small quantities.” Against this background, Derek Hofer is deeply convinced that the company is well prepared for future growth.