Recently, China’s first Lummus polypropylene polymerization reactor, designed and manufactured by Tianhua Institute, was put into operation for the 300,000 t/a polypropylene project of CNOOC Ningbo Daxie Petrochemical Co., Ltd. As the project’s core equipment, the polymerization reactor has been made according to the national standards throughout the process from materials to design. At present, the plant is being operated in a stable status, with key parameters fully meeting the design requirements. The project’s operation marks an important milestone of Tianhua Institute in facilitating the localization and autonomy of the polypropylene reactor.
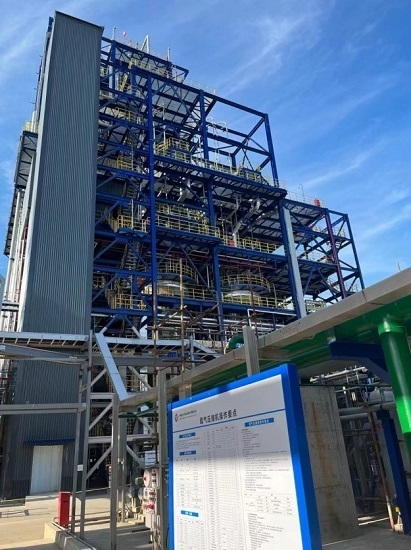
At the site of CNOOC Ningbo Daxie Petrochemical’s 300,000 t/a polypropylene project
The first core equipment
Daxie Petrochemical’s polypropylene polymerization reactor is China’s first Lummus equipment. The Lummus Novolen technology has been among the world’s most licensed polypropylene technologies over the past few years, featuring low total investment, operating costs, high reliability, and the widest combination of products. The process can be used to produce a wide range of polypropylene resins, covering about 60 brands for various purposes. Their advantages come from the core equipment: the polymerization reactor. Two reactors are usually deployed in the entire process. The arrangement of series or parallel connection can be flexibly adjusted according to the production requirements. Therefore, the reactor is the core of the entire Lummus polypropylene plant, with its performance directly affecting the quality of final products.
Serving as an excellent supplier of polypropylene equipment across the country, Tianhua Institute boasts a profound technology reserve in equipment design & manufacturing and strong design capability and manufacturing strength. It offers excellent technological services for domestic polypropylene producers, winning the recognition of domestic and overseas chemical companies. In March 2020, experts from CNOOC Daxie Petrochemical held that Tianhua Institute’s strengths can fully meet the requirements for designing and manufacturing the polymerization reactor, through multiple investigations. They finally selected Tianhua Institute as a designer and manufacturer for the polymerization reactor of CNOOC’s 300,000-ton polypropylene project.
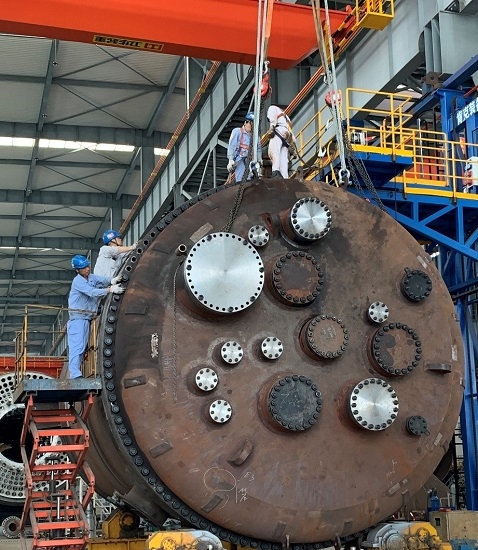
China’s first set of Lummus polypropylene polymerization reactor in Tianhua Institute’s production workshop
Making breakthrough through multi-pronged innovation
In implementing the research task of localizing the key equipment, Tianhua Institute’s project team has reviewed its successful projects and experiences in polypropylene reactions to design and manufacture it. According to the patent licenser’s requirements and the standard differences in homemade and imported equipment, team members consulted and studied domestic and overseas information and conducted research and innovation on the process and equipment. They have solved the problems in equipment design, materials selection, the built-in multi-point temperature-measuring tube, and manufacturing & processing of tungsten alloy parts.
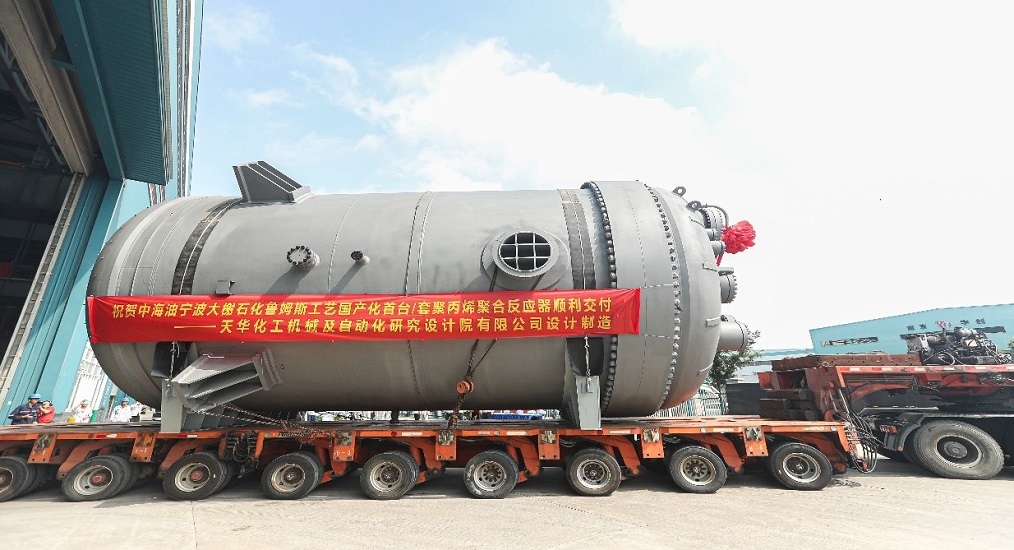
In July 2021, China’s first Lummus polypropylene polymerization reactor, epitomizing Tianhua Institute’s three-year efforts, was delivered, witnessed by representatives of 15 companies, including China Special Equipment Inspection & Research Institute, Shanghai Institute of Organic Chemistry under the Chinese Academy of Sciences, the Lummus patentee, and CNOOC Ningbo Daxie Petrochemical Co., Ltd.
All sides work together to build a workshop
To ensure the installation, Tianhua Institute’s project team installed and commissioned the equipment at the site throughout the process.
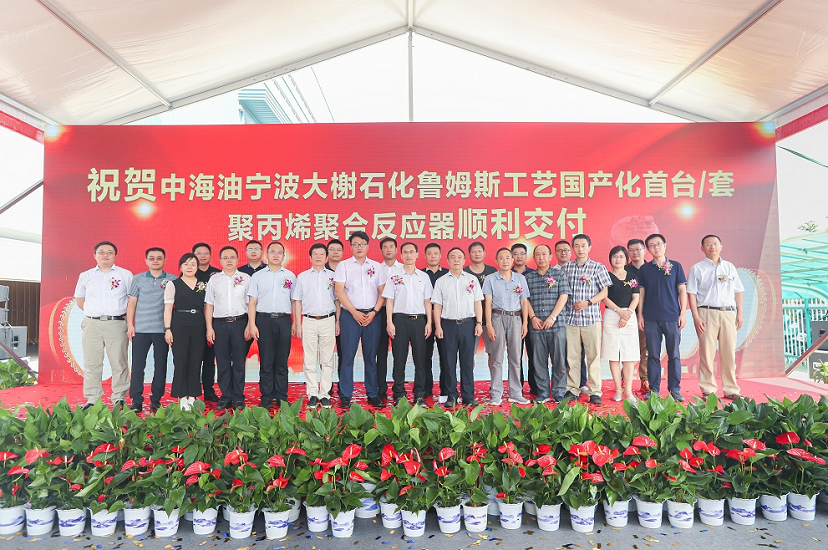
Group photo of representatives from all the departments participating in the project
Confronted with unexpected problems in the manufacturing, CNOOC Ningbo Daxie Petrochemical Co., Ltd. took the initiative to handle them with Tianhua Institute by coordinating all the departments involved in the project.
Through the one-year installation & commissioning, CNOOC Daxie Petrochemical's 300,000-ton plant was operated to produce polypropylene in August 2022, going into production recently.
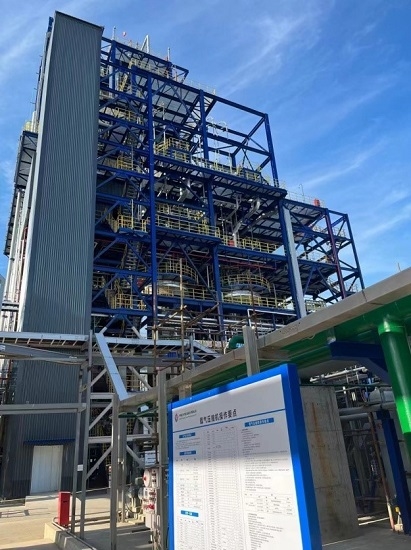
Yin Qingfeng, deputy chief engineer of Sinopec Engineering Construction Co., Ltd. serving as the engineering designer, fully recognized all sides’ collaboration. Yin said that “The success of the polypropylene polymerization reactor, made through the gas-phase process, means that another challenge has been overcome in petrochemical equipment and that the strong synergy of enterprises specializing in engineering design, equipment manufacturing and industrial application has facilitated the breakthrough in the petrochemical equipment technology.”
The reactor’s operation marked that China has met its petrochemical industry’s demand for large, high-end equipment through its design & manufacturing capabilities. The success has filled the gap in domestic design & manufacturing of polypropylene reaction equipment and improved the Institute’s capabilities and core competitiveness in research, design and manufacturing.
More Tianhua Institute-made equipment
In recent years, Tianhua Institute has taken a market-oriented approach, leveraged its technological advantages, explored innovation, and given full play into its proactive role. Committing itself to localizing chemical equipment, it has commercialized multiple technological outcomes, delivering sets of heavy equipment for the chemical industry.
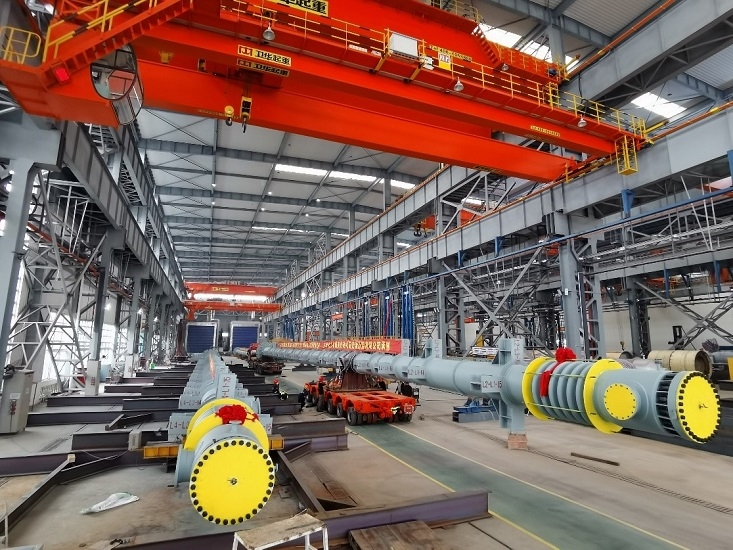
In March 2021, Tianhua Institute delivered its 2×600,000 t/a polypropylene tube reactor to Fujian Zhongjing Petrochemical Co., Ltd. under China Flexible Packaging Holdings Limited. With a weight of 1,720 tons in a single set, the reactor is composed of 16 55-meter-long elbows and eight large 180-degree ones.
In November 2021, Tianhua Institute won the First Prize of China’s National Science and Technology Progress Award for the R&D and industrial application of the complete set of million-ton ethylene technology for complex raw materials.
In May 2022, Tianhua Institute’s steam-based flash-drying and roasting system for ferric phosphate was commissioned successfully in Guizhou Fuquan Phosphorus Chemical’s 40,000 t/a ferric phosphate project, which can be used to enhance the production capacity of ferric phosphate materials for lithium batteries.
In July 2022, Tianhua Institute made a breakthrough in developing its another new product. For ABS resin production, its 18 units of wall-scraping coolers for the external circulation of SAN unit reactors were brought into operation successfully.
In September 2022, Tianhua Institute’s drying & extrusion equipment was used to assist Yulin Chemical, one subsidiary of CHN Energy, in puttting into production the world’s first 10,000-ton PGA degradable material demonstration project.